Samsung's earlier use of a transistor technology could give it an advantage over TSMC at 2nm
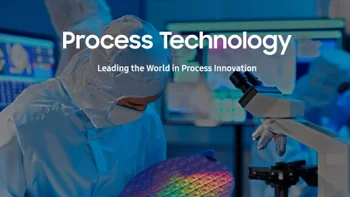
Right now, the top two contract foundries are TSMC and Samsung Foundry with Intel a rising number three. According to DigiTimes, instead of stretching out its 3nm process node for a few years before moving on to 2nm as TSMC is doing, Samsung Foundry is pushing ahead with its research and development on 2nm. Recently, Kye Hyun Kyung, the head of Samsung's Semiconductor and Device Solutions (DS) division, said that within the next five years, Samsung will surpass TSMC and become the world's top foundry.
TSMC is estimated to have a 60% share of the global foundry market
Currently, TSMC has 60% of the global foundry market according to TrendForce. Samsung, which lost Qualcomm's business last year thanks to low yields, is now said to match TSMC's 50-60% yield on 3nm production. However, both firms are believed to be focusing on different things according to semiconductor industry sources. TSMC is looking to maintain a stable level of 3nm capacity while Samsung is looking ahead to next-gen 2nm production.
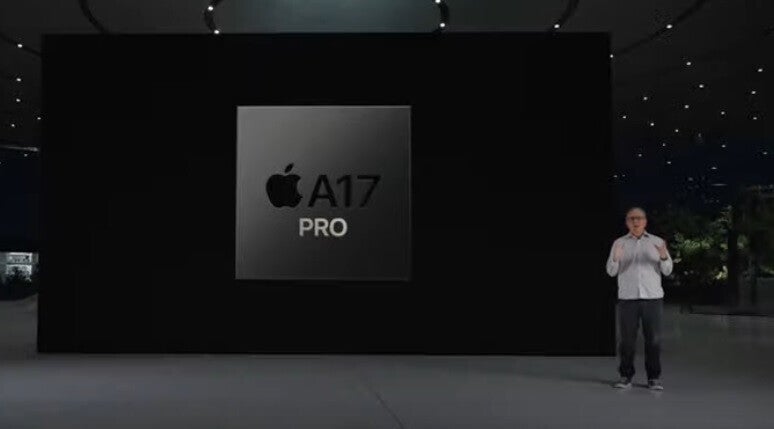
Apple is currently the only smartphone manufacturer shipping a phone with a 3nm chipset
In an effort to snag more customers, Samsung Foundry is expected to get them involved earlier than usual in the process as production schedules are created and Samsung hopes that this entices companies to choose its foundry to turn their designs into chips. South Korea's Money Today says that the industry is expecting the 2nm process to grab the spotlight by 2025.
One area where Samsung is ahead of TSMC is with the use of Gate-All-Around (GAA) technology. Using vertically stacked horizontal nanosheets, these transistors can come into contact with the gate on all four sides resulting in less current leakage and increasing the drive current. While Samsung Foundry is using GAA with its 3nm process node, TSMC continues to use FinFET transistors on its 3nm production. The current number one foundry won't start using GAA until it starts mass-producing 2nm chips in 2025.
Why all of this matters
To put this in layman's terms, the reason why this is so important is that as the process node numbers decline, transistor sizes get smaller. This means that more transistors can fit inside a chip making them more powerful and/or energy efficient.
A look at the last few years of Apple's A-series application processors (AP) is a perfect illustration:
- 2019: A13 Bionic 7nm 8.5 billion transistors (iPhone 11 series)
- 2020: A14 Bionic 5nm 11.8 billion transistors (iPhone 12 series)
- 2021: A15 Bionic 5nm 15 billion transistors (iPhone 13 Series, iPhone 14, iPhone 14 Plus)
- 2022: A16 Bionic 4nm 16 billion transistors (iPhone 14 Pro, iPhone 14 Pro Max, iPhone 15, iPhone 15 Plus)
- 2023: A17 Pro 3nm 19 billion transistors (iPhone 15 Pro, iPhone 15 Pro Max)
While the percentage increase in transistors varies from year to year, and it is getting harder to shrink the size of a transistor, you can see that in the example above, Apple was able to increase the number of transistors inside its A-series chipset by 123%. Put an iPhone 11 Pro Max side-by-side with an iPhone 15 Pro Max and the difference in speed can be felt immediately.
Even if Samsung has a head start at 2nm because of its early implementation of GAA, Apple has been TSMC's largest customer for years and we wouldn't expect to see the gang in Cupertino switch the supplier of what is possibly the most important component used to make an iPhone.
Samsung manufactured Apple's A-series chips up until the A8 which was produced for the iPhone 6 and iPhone 6 Plus by TSMC in 2014. The A9, designed for the iPhone 6s and iPhone 6s Plus, was built by both TSMC and Samsung in 2015. It should be noted that by this time, both Apple and Samsung were embroiled in a nasty patent battle with Apple looking to reduce its use of Samsung as a supplier for the iPhone. For the A10 chip designed for the iPhone 7 line, Apple selected TSMC to manufacture its AP and has stuck with the foundry since then.
Things that are NOT allowed: