NYU student works undercover at Pegatron assembling the Apple iPhone 7
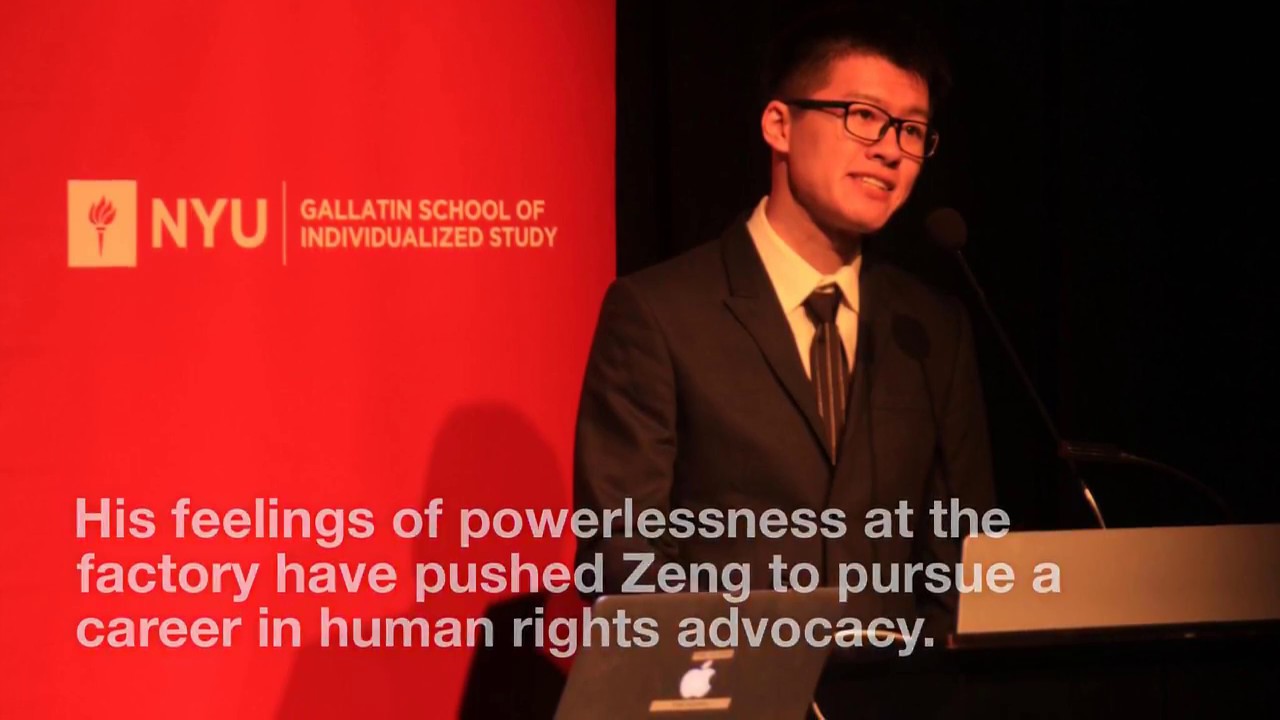
Ever wonder what it might be like to work at a factory, assembling the Apple iPhone 7? New York University student Dejian Zeng found out. He spent last summer working undercover at a Pegatron plant in China for an NYU project. What he discovered was that it is not a glamorous job, and those employed in these factories are not getting rich by working there. He was put to work right on his first day when he was given the tasks of affixing a sticker and adding a screw to the Apple iPhone 6s.
While Zeng was working at the factory, production shifted from the Apple iPhone 6s to the Apple iPhone 7, and that is when draconian security measures were put in place. The sensitivity of the metal detectors was hiked and employees were forced to go through two security checkpoints. As a general rule, Personal phones and other electronics are not allowed in the factory.
Workers start out as operators and move into the multitask position. The next two levels up include the group leader and line manager. Then there is the section manager, the division manager and factory director. Most don't hang around long enough to get promoted to a high position. Overtime is often mandatory, and workers are not allowed to play music to help them get by the repetitive motions of their boring jobs.
Rumors that workers put in long hours for little pay happen to be true. Including overtime. Zeng was working 12 hours a day, but getting paid for only 10.5 hours daily because of unpaid breaks. Apple, known to the workers as "the client," had employees visiting the factory daily once production switched to the iPhone 7 to make sure things were going smoothly. Apple also monitored the workers to make sure that no one worked more than 60-hours a week.
For all of that hard work, the NYU student couldn't even afford the device he was assembling. His pay amounted to $450 a month. This explains the high turnover rate, and why some workers don't last more than a couple of weeks before quitting. It also explains why most employees who work at the factory producing the latest iPhone models, end up owning personal smartphones made by lower priced Chinese manufacturers like Oppo.
"At the beginning, I was assigned to the assembly line in the department called FATP, final assembling testing packing. We put the iPhone together. One line might have about 100 stations. Each station does one specific thing. At the beginning, I work on iPhone 6S. And then after August, we are working on iPhone 7. When I'm working iPhone 6S, I do two stations. One station at the beginning I did fastening speaker to housing. What I did is that I put the speaker on the case, and I put a screw on it. The [iPhone] housing — we call it the back case — is moving on the assembly line, and that's when we pick it up, and now we get one screw from the screw feeder, and then we put it on the iPhone and then put it back, and it goes to next station.-Dejian Zeng, student, NYU
As for Zeng, the experience led him to pursue a career in Human Rights Advocacy. For more on Zeng's experience, click on the video found at the top of this story.
source: BusinessInsiders, NYUWagner
Things that are NOT allowed:
To help keep our community safe and free from spam, we apply temporary limits to newly created accounts: