Making the HTC U11: from design to assembly, a smartphone is born
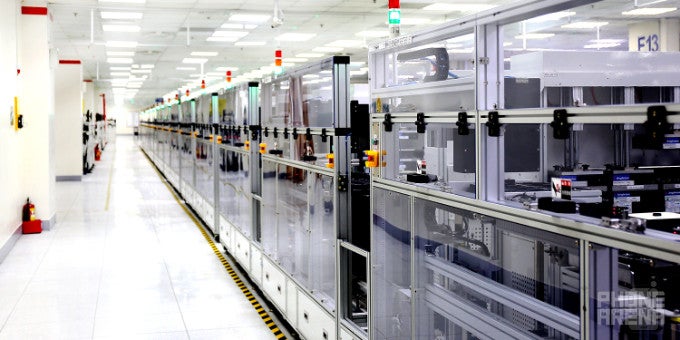
Today's a very special day for HTC. Not only is the company launching its latest flagship smartphone, the new U 11, but the manufacturer is passing an important milestone, celebrating 20 years in the business. That's brought us lots of memorable handsets like the Android-introducing HTC Dream, and the jack-of-all-trades HD2, all the way up to today's modern portable powerhouses.
To help usher-in the era of the U 11 and its next 20 years making mobile devices, HTC invited us to Taiwan as it opened its doors to journalists for an unprecedented look at how the company creates its smartphone designs, innovates with the latest technologies, and ultimately puts all that hardware and software together to roll a finished phone off the assembly line.
You might think that creating a smartphone is the most straightforward thing in the world: just get all the latest and greatest parts, assemble them together into a pocket-friendly rectangle, and you've got a next-gen handset. Easy peasy, right? If only things were that easy.
HTC's phones get started in its design studios, located both here in Taiwan and San Francisco. There, creative minds with a range of backgrounds, from industrial design to UI creation, come together to contribute ideas for the company's next phones.
It takes a lot of experimentation before HTC nails the look and features it wants to deliver with a certain phone, and not all of those ideas pan out. One scrapped idea we got to see emerged back when gaming-phones looked like they might be the next big thing, and featured a landscape-slider design that had a pop-out D-pad for precise game controls.
While that phone never saw the light of day, other designs go back to the drawing board over and over as HTC continues to refine its vision, and we ultimately end up with a handset ready to move forward as one of the company's next commercial models.
HTC uses an open floorplan for its design studios, and that's key to collaboration. This is important because not everyone's ideas are initially going to align, and there's a lot of give-and-take when it comes to deciding what's most important to make a new phone great. One designer might push for a big battery to give users day-long endurance, while another might be interested in a super-slim profile. Not everyone can get what they want, but by finding the right compromises (and testing iteration after iteration), HTC tries to arrive at the ideal balance.
Creating a design
You might think that creating a smartphone is the most straightforward thing in the world: just get all the latest and greatest parts, assemble them together into a pocket-friendly rectangle, and you've got a next-gen handset. Easy peasy, right? If only things were that easy.
HTC's phones get started in its design studios, located both here in Taiwan and San Francisco. There, creative minds with a range of backgrounds, from industrial design to UI creation, come together to contribute ideas for the company's next phones.
We were greeted by an expansive display of the HTC's phones over the years, laid out in a spectrum of colors, but the really interesting hardware was hiding away beneath, tucked away in secret drawers: the design prototypes.
It takes a lot of experimentation before HTC nails the look and features it wants to deliver with a certain phone, and not all of those ideas pan out. One scrapped idea we got to see emerged back when gaming-phones looked like they might be the next big thing, and featured a landscape-slider design that had a pop-out D-pad for precise game controls.
While that phone never saw the light of day, other designs go back to the drawing board over and over as HTC continues to refine its vision, and we ultimately end up with a handset ready to move forward as one of the company's next commercial models.
Blending design with technology
Choosing the right design for your next smartphone is a critical step towards making that vision real, but just as important is making sure that this impressive-looking phone is also an impressively capable handset. That requires lots of R&D work, and after stopping by HTC's design studio, we headed around the corner to check out its lab facilities.
In its camera facilities, HTC engineers customize the phone's imaging algorithms to deliver the most natural-looking results possible. That means calibrating exposure against a number of reference light sources, as well as evaluating white-balance performance under different kinds of illumination. Once the company thinks it's come up with software that squeezes the most performance possible out of available image sensors, those engineers test their results on dozens of individual sensors to make sure that the results are consistent across all that hardware.
Other equipment present here evaluates tech like optical image stabilization, shaking a camera while trying various shutter speeds to push performance as far as it can go.
Next door, HTC's audio team is hard at work on its latest BoomSound developments, optimizing speaker design and performance. Speaker components are tested in an isolation chamber to verify consistent output with minimum distortion, and in addition to this physical testing, the company's engineers also work with computer modeling to see how slight changes to speaker enclosures change the way that sound reaches our ears.
Speaking of which, once a design is ready to be tested in a physical handset it's on to HTC's anechoic chamber, where the company uses a simulated human torso complete with detailed ear canal to evaluate how that phone sounds when held at various angles – from right up against the head to casually out to the side. And while that anechoic chamber helps produce some nice clean audio data, HTC also wants to see how its speakers work in real-world situations, so a second room reproduces ambient sounds ranging from an office, to a cafe, to a busy street – and similarly evaluates how the phone would sound to its user.
The birth of a new smartphone
Once everything from the design to the tech is finalized, it's time to build a smartphone. For that, we head down the highway to HTC's manufacturing plant. While the idea of a big-name smartphone-maker like HTC might have you picturing a sprawling industrial plant, the actual facilities are quite nondescript, and look like a typical office building from outside.
An HTC phone comes together in two main stages, each on a separate floor of the company's facility. First, the phone's circuitry is produced. That starts with a raw printed circuit board, and because the boards in each phone are so small, in order to more easily work with them they start out as the boards for four phones, all joined together.
As these boards pass down the assembly line, robotic arms start placing all the components that will populate these boards in the right places. The parts themselves, from the main processor to every little tiny transistor arrive on giant rolls – almost like a movie filmstrip. Once they're all in place, a quick trip through the soldering station brings them all together, nice and secure.
An HTC phone comes together in two main stages, each on a separate floor of the company's facility. First, the phone's circuitry is produced. That starts with a raw printed circuit board, and because the boards in each phone are so small, in order to more easily work with them they start out as the boards for four phones, all joined together.
As these boards pass down the assembly line, robotic arms start placing all the components that will populate these boards in the right places. The parts themselves, from the main processor to every little tiny transistor arrive on giant rolls – almost like a movie filmstrip. Once they're all in place, a quick trip through the soldering station brings them all together, nice and secure.
Then it's time to verify that everything's functioning properly. HTC's robotic arms submit each board to a visual inspection (with the help of computer-connected cameras), a logic test that ensures all the circuitry is behaving as expected, and a radio test, to make sure that your phone will work with your cellular provider. When everything's looking good, the finished circuit boards are ready to head upstairs for phone assembly.
While board production is largely automated, phone assembly involves a lot more human interaction, Boards are placed in the phone housings, along with components like the screen, buttons, USB connectors, and the rest of the handset's hardware. Robots also lend a hand here, automating steps like applying glue that helps ensure a water-tight construction.
Each handset goes through a battery of tests. This ranges from everything from Bluetooth connectivity, to flashlight calibration, to testing water-resistance. Interestingly, for that HTC doesn't actually use water, but instead employs air pressure to check for leaks.
One of the more surprising tests we got to see was a tumble test. Each new handset is put in a protective case and knocked around inside a large drum, ensuring that everything is still working even after some rough handling. The case helps keep the phone looking new, but it's still a bit of a shock to see every phone subjected to such a very physical process.
Once everything is working well, it's time to program each phone with the firmware for its particular region and carrier, and then get started with packaging. Here, the new phone is joined with its accessories, paperwork, and everything else you'll find in its box – then weighed on an extremely precise scale to ensure that nothing's missing. Finally, the finished, boxed phones roll off the assembly line and are joined in a pallet with dozens of their siblings.
Even now, things aren't over, and after that array of automated tests, HTC randomly subjects handsets from these batches to in-depth human testing, to make sure that nothing was missed and no sub-standard handsets get through. If one unit from a batch looks bad, the whole pallet is suspect, but if everything checks out, it's time to prepare for shipping and get these new phones out to carriers and retailers where they're ready for you to buy.
Each handset goes through a battery of tests. This ranges from everything from Bluetooth connectivity, to flashlight calibration, to testing water-resistance. Interestingly, for that HTC doesn't actually use water, but instead employs air pressure to check for leaks.
One of the more surprising tests we got to see was a tumble test. Each new handset is put in a protective case and knocked around inside a large drum, ensuring that everything is still working even after some rough handling. The case helps keep the phone looking new, but it's still a bit of a shock to see every phone subjected to such a very physical process.
Once everything is working well, it's time to program each phone with the firmware for its particular region and carrier, and then get started with packaging. Here, the new phone is joined with its accessories, paperwork, and everything else you'll find in its box – then weighed on an extremely precise scale to ensure that nothing's missing. Finally, the finished, boxed phones roll off the assembly line and are joined in a pallet with dozens of their siblings.
Actually seeing a smartphone come together like this is an incredibly impressive experience, and that's made all the more so by how effortless HTC makes everything look. The assembly lines are so clean and straightforward that it's enough to have you thinking that you could buy some smartphone-making machines and set up shop for yourself; of course, it takes a ton of work to even get a phone to this assembly stage, and the efforts of hundreds of people at every step of the process.
Thanks to HTC for giving us this special look at how it makes its phones. It's one thing to use a new smartphone, but seeing how it came into existence really gives you a new-found appreciation for just how amazing these tiny little supercomputers are.
Things that are NOT allowed: